Service center
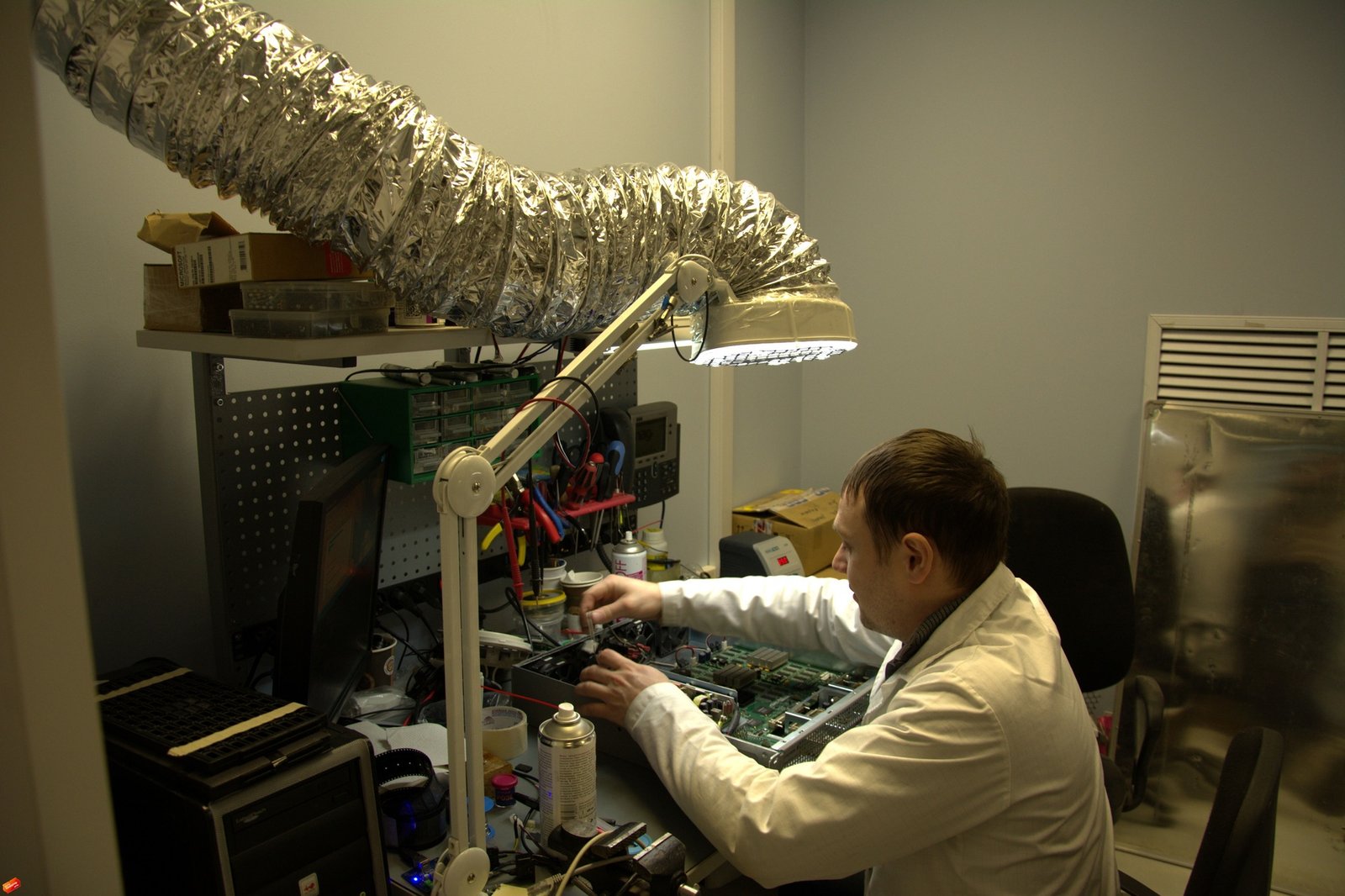
service center
A couple of weeks ago in our blog already flashed a publication about the service center of the company “NAG”. However, after reading the resulting material again, the guys from the service center felt that the text turned out to be somewhat compressed and not fully revealing the workflow. So today, as they say, take two. We will write more detailed and accessible.
The “NAG” specializes in servicing, warranty and post-warranty repair of the widest range of telecommunications equipment.
So, in order for the equipment to fall into the hands of our engineers, it needs to pass registration in the database. There, each device is assigned an identification number, which is subsequently labeled with iron. In the future, due to this number, the client will be able to track the status of the order execution.
The operator of the service center is responsible for processing and corresponding registration of the equipment. His duties include the preparation of documentation for equipment, inventory of the equipment kit, photo or video, fixing the state and subsequent organization of storage of equipment before transmission for repair.
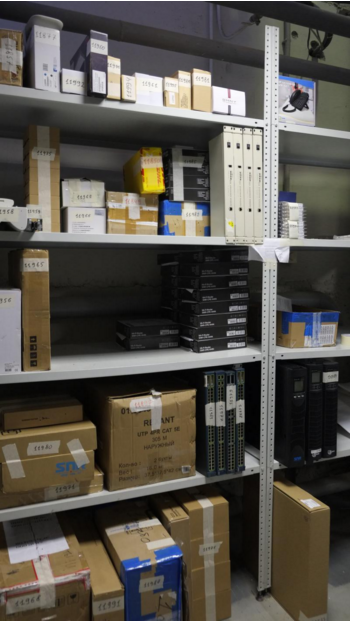
His fate, iron awaits in the warehouse for a short time and gets into the engineering zone. First of all, the center specialist will conduct all the necessary diagnostic work, during which the malfunction is determined, and the possibility of its elimination is estimated and the spare parts necessary for repair are determined.
The workplaces in our service center are equipped with everything necessary for fruitful work. Antistatic protection and grounding are installed. Specialists always have soldering stations of different types and characteristics at hand. From harmful vapors, formed during the soldering of microcircuits, a special extract is saved. To test the equipment in the service are installed special racks. Here, user equipment, routers, switches, servers, UPSs and much more are tested.
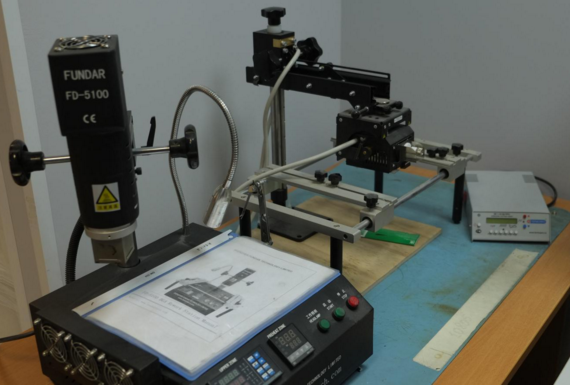
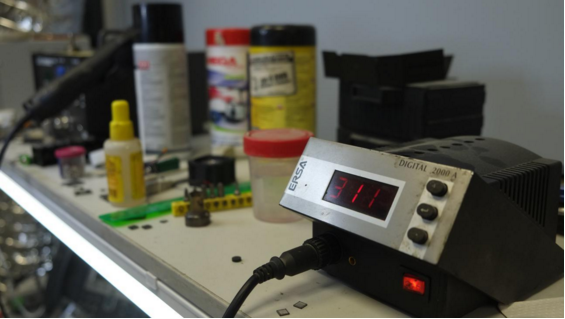
]
