3D
In anticipation of the massive sales of the new PICASO 3D Designer X PRO, the question becomes more urgent: how this 3D printer differs from numerous colleagues, what features of work on it and it will look like in practice. With these questions, we turned to the representatives of PICASO 3D, who kindly shared information.
The printer is equipped with several new systems that are designed to significantly improve the print quality, so And ensure the convenience of working with it. Among these innovations are systems responsible for: control of the supply of plastic, automatic alerts on the operation of the device, control of the first layer, profiles of work with different materials, network printing and accurate autocalibration. Each of them will be described in more detail below.
The print head of the printer (hereinafter – PG) is equipped with the updated technology JetSwitch, which proved to be well in the previous model Designer PRO 250. Let’s explain for those who are not familiar with this technology : The technology allows the use of two materials at the same time for work – a valve is provided in the SG design that instantly blocks the supply of one of the materials, without the need for cooling, which makes printing two materials simultaneously cleaner and much faster.
Upgrading JetSwitch now has two print modes. In one of them, which is enabled by default, using the integrated nozzle cleaning system, you can confidently print even the thinnest elements, making it ideal for complex presentation and detailed printing.
The switching speed between materials is 5 seconds .
The second printing mode is accelerated. The switching speed between the materials in this mode is less than one second. Due to this, the speed of printing parts with support and printing of two colors is significantly increased. This mode is more suitable for printing large-sized objects with walls thicker than one millimeter.
The rest – further, in order.
The control system for plastic flow
PICASO 3D Designer X PRO is equipped with sensors (encoders) that control the slippage of the yarn in the plastic feeding system. The printer constantly “counts” how much plastic passes through the extruder per unit of time. What does this give? The use of such a solution helps to avoid many cases of defective printing, and thus unnecessary loss of material, time and nerves. Now if the plastic or nozzle runs out, Designer X PRO automatically detects the problem and tries to fix it by itself, using the built-in nozzle clearing algorithm.
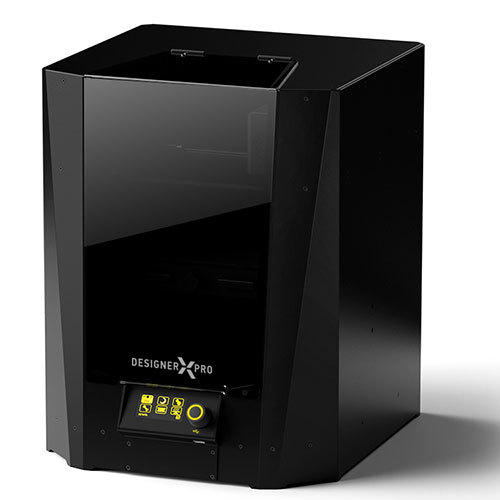
If the problem is solved after automatic cleaning, the printer will continue to work and notify the user that there were difficulties in the printing process. This will help to draw attention to this situation and avoid its recurrence.
If automatic cleaning does not work, the Designer X PRO will pause printing and inform the user, using the built-in notification system, about The situation that has arisen. The user can manually clean the print head, replace the material, or replace the nozzle. Once the problem is resolved, the printer will be able to continue working without loss of print results, material and time.
Continuous feed monitoring helps to avoid situations where the plastic has already run out of the coil and the printer has not finished the model building yet. It is not possible to change the plastic Designer X PRO independently, but it is already possible to send a signal to the user about the occurrence of the problem.
Alert System
As we said, Designer X PRO not only controls its state, but also shares this information with the user. Changing the color of the backlight of the working chamber, the device will tell you: at what stage the print is located, whether any difficulties have arisen in the course of operation and whether user intervention is required. If you have an Internet connection, the device will be able to notify you of its status, even if you are not near the printer. Controllability and predictability of the process is one of the most important features of the new Designer X PRO.
The first layer control system
Anyone who has ever used a 3D printer knows about the importance of the first layer. It’s like a foundation. If the foundation is uneven or unstable, then the whole building will collapse sooner or later. So in 3D printing – badly entrenched on the platform or uneven first layer, with a very high probability, will destroy the entire printout. The difficulty lies in the fact that for different types of plastic pressing against the printing platform needs a different. Thanks to the feedback system, in each case, the Designer X PRO achieves an optimum clamping force.
When starting the print job and first touching the table nozzle, the printer, by means of a built-in PG encoder and using the pre-set for each material the resistance profile of the first layer, measures the speed of the filament movement and almost instantly corrects the position of the table along the Z axis for the optimal construction of the first layer.
The system of profiles
Thanks to the new profile system, Designer X PRO “knows” which material is currently installed in which nozzle of the printer. This solves at once a whole complex of possible problems that can arise due to improper adjustment by type of material – in preparation for printing or when changing over, after changing material. Now, after loading the filament into the printer, when preparing a print job, there is no need to set the temperature separately, the feedrate separately, etc. – Once you have prepared a profile for each material and saved it in the printer, you can print with any similar material, without wasting time on the preparation of a new job.
Network printing
Networking is not just the ability to remotely receive alerts from the printer. This is a function that allows you to combine several Designer X PRO into a single structure that is managed from one computer using the updated Polygon X program. Monitor printing, track installed materials, create job queues, assign them to devices, schedule work schedules, track alerts from all devices in A single interface – now all this can be done promptly, without getting up from the workplace.
Extruder with Jet Switch technology
The renewed Jet Switch extruder is an extruder with two nozzles, which allows to print with two materials and instantly stop feeding one of them without lowering the temperature. The modified new version of the extruder, due to the change in the internal device, has a high quality of printing, increased productivity and resistance to blockages.
Technical characteristics:
Print material: PLA, ABS, PLA Flexible, PVA, PC, Hips, Nylon, Laywood, FilaFlex, Filamentarno.
The diameter of the thread: 1.75 mm.
Printing area: 200 x 200 x 210 mm.
Housing material: Aluminum (composite).
Guides (steel): X and Y – rail, Z – cylindrical.
The thickness of the layer: from 0.05 to 0.25 mm, is regulated through the software.
Positioning accuracy: XY: 11 microns, Z: 1.25 microns.
The presence of a heated platform: Yes.
Printing platform: Aluminum and glass.
The number of print heads: 2.
Automatic calibration table:. Yes
Nozzle diameter: 0.3 mm
.
The maximum working temperature of the extruder is 380 ° C.
The maximum working temperature of the working platform is 140 ° C.
Noise level: 55 dB.
Control board: based on ARM CORTEX M4 32 bit STM.
Interfaces: USB, Ethernet, USB Flash (drive in the set).
Compatible with OS: Windows XP, Windows 7, Windows 8-10.
Printing speed: up to 30 cm3 / hour.
Supported formats: STL, PLG.
Software: PICASO 3D Polygon XOperating ambient temperature: 15 ° – 32 ° C.
Dimensions: 492x390x430mm;Weight: 16kg.
Dimensions and weight in the package: 690 x 500 x 470, 22kg.
Power consumption: 220V + – 15% 50Hz (available option 110 V + -15% 60Hz) 400W.
Warranty: 2 years.
As we can see, the new PICASO 3D Designer X PRO differs significantly not only from 3D printers of other manufacturers, but also from its predecessor – PICASO 3D Designer 250 PRO. In the very near future we will be able to see this in practice and be sure to share our impressions.
Consider closer
And now the most interesting! The new Designer X PRO contains many new features: an easy-detachable magnetic table, directional material feeding, new construction materials and other interesting solutions.
XPRO supports the printing of a variety of materials, including PLA, PVA, flex, rubber, relax and even carbon.
This sample was printed on PICASO DESIGNER XPRO with different materials:
Consider this machine and other samples closer, and see the new printer in operation You will be one of the first – at the upcoming exhibition and conference Top 3D Expo 2017, which will be held April 14 in Moscow.
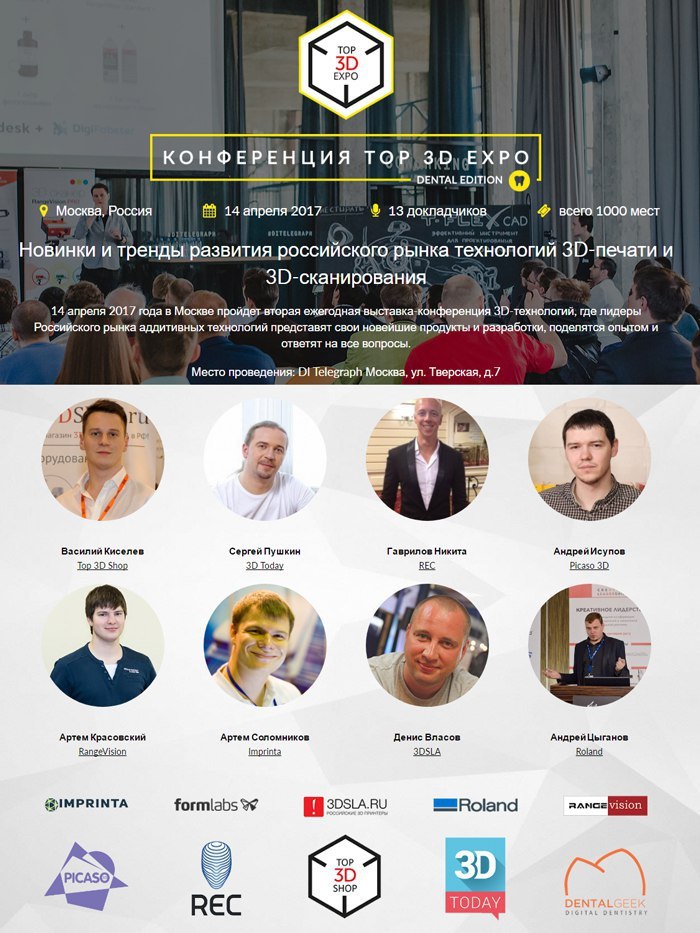
